Master Scheduling and the Due Dates for Safety Stock Requirements in Microsoft Dynamics AX & 365 for Finance and Operations, Enterprise
Master Scheduling and the Due Dates for Safety Stock Requirements in Microsoft Dynamics AX & 365 for Finance and Operations, Enterprise
Safety stock requirements often represent a critical element in the Sales and Operations Planning (S&OP) game plans for stocked products. For example, the safety stock quantity can be used to anticipate demand variations in S&OP games plans for end-items with demand forecasts and period lot-sizing logic, or it defines the minimum quantity when using Min/Max logic. Safety stock may also reflect an inventory buffer for key components of manufactured items, or for different warehouses in a multi-level distribution network.
In Microsoft Dynamics 365 Finance and Operations, Enterprise edition (termed D365FOE for short) and in previous versions of Dynamics AX, the safety stock due dates and quantities are reflected in the calculation of net requirements by master scheduling logic and in the generation of planned orders and action messages that provide meaningful information for decision making by planners and buyers. All too often, the inappropriate assignment of these due dates leads to confusing information for planners and buyers, and reduced effectiveness in coordinating supply chain activities.
This article reviews the four basic approaches for defining the safety stock due date in D365FOE using the "Fulfill Minimum" options. It also describes an alternative approach using the "Minimum Key" capabilities. It provides suggested guidelines about when to use each approach, and case studies illustrate the suggested guidelines. These considerations are reflected in the following sections within the article.
- Four Basic Approaches for defining the Safety Stock Due Date
- Basic Approach #1: Safety Stock Due Date of "Today's Date + Procurement Time"
- Basic Approach #2: Safety Stock Due Date of "Today's Date"
- Basic Approach #3: Safety Stock Due Date of "First Issue"
- Basic Approach #4: Safety Stock Due Date of "Coverage Time Fence"
- Alternative Approach: Safety Stock Due Date based on the "Minimum Key" Capabilities
- Summary
The five approaches apply to the current version of D365FOE as well as previous versions of Dynamics AX, since the functionality has not changed across the different versions. To illustrate this point, the screenshots within the article reflect the user interface in Dynamics AX 2009 as well some examples of the D365FOE user interface.
To simplify the explanation and screenshot examples, it is assumed the item identifier consists of just the item number, and coverage planning applies to the site/warehouse. This represents a dominant business model for many AX/D365FOE implementations. However, the same concepts apply when the item identifier and coverage planning include other dimensions such as color, size and/or configuration.
The use of safety stock requirements was covered in previous articles, such as the use of safety stock in S&OP game plans and the calculation of a safety stock quantity. It was also covered in my recent book about master planning using Dynamics 365 for Operations.
1. Four Basic Approaches for defining the Safety Stock Due Date
The Fulfill Minimum policy for an item and warehouse (defined as part of the Item Coverage information) provides four basic approaches for defining the safety stock due date. Figure 1 illustrates this policy for the item "Z_Product1" and warehouse "MAIN", with the safety stock quantity of 111 and a coverage group of "Period 14" that reflects period lot-sizing logic. The bottom of the figure lists the options and an estimated applicability percentage for each. The next four sections provide further explanation of each option for the Fulfill Minimum policy.
Figure 1. Example of the Item Coverage Form and the Fulfill Minimum Options

In most scenarios (with estimated applicability of >80%), the option for "Today's date + procurement time" provides a due date that results in the appropriate calculation of net requirements and meaningful planned orders and action messages. The options for "Today's date" and "First Issue" work in certain scenarios, and the last option is rarely used. Many scenarios can benefit from an alternative approach using the "Minimum Key" capabilities, as described in a subsequent section.
2. Basic Approach #1: Safety Stock Due Date of "Today's Date + Procurement Time"
The concept of a safety stock due date based on an item's lead time has been fundamental for Min/Max logic, where the minimum quantity represents average daily usage multiplied by the number of lead time days. The same concept also applies in S&OP game plans employing safety stock requirements to anticipate demand variations, to provide inventory buffers for key components, or to provide inventory buffers for warehouses in a multilevel distribution network.
This approach is generally applicable in most scenarios. It is not applicable in certain scenarios because the item's lead time does not provide the relevant safety stock due date. One example involves a due date that needs to reflect a cumulative lead time or a user-specific offset, as illustrated by Case 4, Case 5 and Case 6 in a subsequent section.
The basis for an item's lead time varies for a purchased item, a manufactured item and transfers, as described below. It is also affected by the number of days for safety margins such as a receipt or issue margin, and whether they reflect working days or calendar days.[1]
- Procurement Time for a Purchased Item. The lead time for a purchased item can be expressed in calendar days or working days. For a given item, it is defined as a companywide or site-specific policy (on the Purchasing Tab of the Default Order Settings form) and optionally overridden as a site/warehouse-specific policy (on the Item Coverage form).[2] The safety stock due date will reflect the number of days of this procurement time.
- Procurement Time for a Manufactured Item. The "fixed" lead time for a manufactured item represents the average elapsed time for production regardless of order quantity and capacity considerations. This lead time can be expressed in calendar days or working days. For a given item, it is defined as a companywide or site-specific policy (on the Inventory Tab of the Default Order Settings form), and optionally overridden as a site/warehouse-specific policy (on the Item Coverage form). The safety stock due date will reflect the number of days of this procurement time.
The "fixed" lead time for a manufactured item can serve other purposes, and its significance varies depending on whether or not routing data is used. A separate article provides further explanation about the significance of inventory lead time for manufactured items. - Procurement Time for a Transfer. This is typically defined as the transportation time between a warehouse pair, although it can be optionally overridden as a site/warehouse-specific policy for an item (on the Item Coverage form). The safety stock due date will reflect the number of days of this procurement time.
Case 1: Safety Stock Requirements for a Make-to-Stock Manufactured Item
A manufacturer defined the demand forecasts and safety stock requirements for stocked end-items, and the associated routing data for each item. The lead time for each item's production order was calculated based on the routing data. In addition, they specified the inventory lead time for each end-item (typically 3-7 days) so it could be used in determining the safety stock due date.
3. Basic Approach #2: Safety Stock Due Date of "Today's Date"
The Fulfill Minimum option of "Today's Date" only applies to certain scenarios, where the value of "today's date" reflects the date on which Master Scheduling was performed. Case 2 illustrates one of these scenarios, and the option is also employed in the Minimum Key approach described in Section 5. It does not apply in most scenarios because the safety stock due date will occur before other demands such as sales orders or forecasts, thereby indicating it has a high priority.
Case 2: Safety stock for products with a short sales order lead time
A manufacturer of consumer products received EDI sales orders with guaranteed delivery within 3 days, where the cumulative lead time for these products exceeded 2 months. As part of the S&OP game plans for these products, they employed demand forecasts and safety stock requirements (which covered unexpected spikes in demand). They used "today's date" as the safety stock due date because they needed to be ready for any demand spikes. The safety stock requirements were almost as important as the sales order demand.
4. Basic Approach #3: Safety Stock Due Date of "First Issue"
The user documentation explains this due date option as "the specified minimum quantity is met on the date of the first issue that is scheduled during the time period that is specified in the Coverage time fence field." Stated another way, the due date will reflect the first requirement for the item. In those scenarios where a planned supply order will be trigged by the first requirement (such as an actual sales order), it would make sense to align the safety stock due date so that the planned order quantity could reflect the required quantity plus the safety stock quantity. Case 3 illustrates this scenario.
As one potential problem with this approach, the safety stock quantity will never be considered until there is a requirement, so that you may not have safety stock inventory in advance of demand.
Case 3: Include Safety Stock Requirements in next Production Order to meet Sales Order Demand
An industrial products company had several products with low sales volumes and intermittent demand. They did not warrant a demand forecast, and their S&OP game plans employed Min/Max logic. In cases where sales order demand drove inventory below the minimum quantity, they wanted to align the safety stock due date with the sales order ship date. In this way, the planned production order quantity covered both the sales order and safety stock demands.
5. Basic Approach #4: Safety Stock Due Date of "Coverage Time Fence"
The user documentation explains this due date option as follows: "the specified minimum quantity is met during the period that is specified in the Coverage Time Fence field." Stated another way, the due date will reflect the end of the planning horizon for the item. In most scenarios, this simply provides visibility of the safety stock requirement but does not result in meaningful planned orders.
My research suggests this due date option is not commonly used. Even though a Coverage Time Fence can be specified for an item (based on policies within the Coverage Group assigned to the item), I cannot think of an applicable use case for this option.
6. Alternative Approach: Safety Stock Due Date based on the "Minimum Key" Capabilities
The capabilities associated with a Minimum Key are not widely used or understood. However, they provide an innovative alternative for assigning safety stock due dates, as described in this section. This section does not cover all possible capabilities and uses of the Minimum Key.
As an explanatory approach, it is easiest to start with an example. Figure 2 provides an example of the Item Coverage form and the fields related to the Minimum Key approach to a safety stock due date. The top of the figure displays the Overview Tab of the Item Coverage form for the item "Z_Product2" and warehouse "MAIN", and a safety stock quantity of 111.
Figure 2. Example of the Item Coverage Form andthe Minimum Key Approach to Safety Stock Due Dates
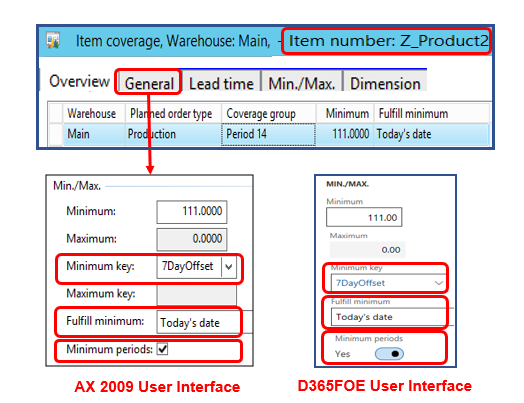
The bottom of Figure 2 displays information on the General Tab, and highlights the three critical fields for using the Minimum Key approach. This includes the Minimum Key identifier and the related checkbox for "Minimum Periods", and the Fulfill Minimum option of "Today's date".
You define a Minimum Key on the Minimum/Maximum Keys form, as illustrated in Figure 3. For our purposes, the user-defined identifier of a Minimum Key indicates the number of offset days that determine the safety stock due date, and the actual offset is defined by the related "period information". The left side of Figure 3 illustrates several Minimum Key identifiers, and the right side illustrates the period information for the "7DayOffset". The factor of "1" for day 7 indicates the desired safety stock due date relative to today's date. This approach represents a floating due date, whereas other uses of a Minimum Key might employ a fixed date.
Figure 3. Example of the Minimum/Maximum Keys form

An example of the Net Requirements form provides confirmation of the Minimum Key approach to safety stock due dates. The top of Figure 4 displays the Overview Tab identifying the item "Z_Product2" and warehouse "MAIN", with the safety stock quantity of 111 and a coverage group of "Period 7". The middle of the figure displays the safety stock due date of 1/21/2018, which reflects the "7DayOffet" and today's date of 1/15/2018. The bottom of the figure displays the pegging information for the first planned production order, which has been generated based on the "Period 7" lot sizing logic for covering the demands stemming from a sales order, safety stock and sales forecast.
Figure 4. Example of the Net Requirements form and the safety stock due date based on the Minimum Key Approach

Case 4: Safety stock due date reflects a cumulative lead time
The master schedulers at a manufacturing company used demand forecasts and period lot-sizing as part of the S&OP game plans for end-items. They also wanted to place safety requirements at a future date that represented the cumulative lead time across several BOM levels. This could not be modeled by the option for "Today's date + procurement time", so they employed the Minimum Key approach to indicate the desired due date reflecting a cumulative lead time.
Case 5: Safety Stock Requirements for an off-site Finished Goods Warehouse
Many of the end items for an industrial products company were produced at one warehouse representing the manufacturing plant, and then immediately transferred to a nearby finished goods warehouse for subsequent shipment to customers. The transportation time was modeled as one day, whereas the items' production lead time was typically 5 days. As part of the S&OP game plans for these products, they defined demand forecasts and safety stock requirements at the finished goods warehouse. In order to correctly identify the desired safety stock due date, they realized that the option for "Today's date + procurement time" did not provide a workable solution because the transfer lead time of one day was too short. They wanted a 7 day offset to reflect production considerations. As a result, they employed a Minimum Key for a "7DayOffset" as a solution approach.
Case 6: Safety Stock Requirements for Key Components of Stocked Products
An equipment manufacturer had several key purchased components where any type of vendor problem (such as a shutdown) would seriously impact their production. To avoid this potential problem, they defined safety stock requirements for these components. In order to correctly identify the desired safety stock due date, they realized that the four basic approaches would not work, and they employed the Minimum Key as a solution approach.
7. Summary
Safety stock requirements often represent a critical element in the S&OP game plans for stocked products. The required quantities and due dates are reflected in the calculation of net requirements by master scheduling logic, and in the generation of planned orders and action messages that provide meaningful information for decision making by planners and buyers. All too often, the inappropriate assignment of these due dates leads to confusing information for planners and buyers, and reduced effectiveness of SCM coordination.
This article reviewed several approaches for defining safety stock due dates, including the four basic approaches provided by the "Fulfill Minimum" options. In some cases, these basic approaches do not provide the desired due date, and the article described an alternative using the "Minimum Key" capabilities. It provided suggested guidelines about when to use each approach, and case studies illustrated the suggested guidelines.
Comments
Post a Comment