The 8 Best Order Picking Methods (Including Batch Picking)
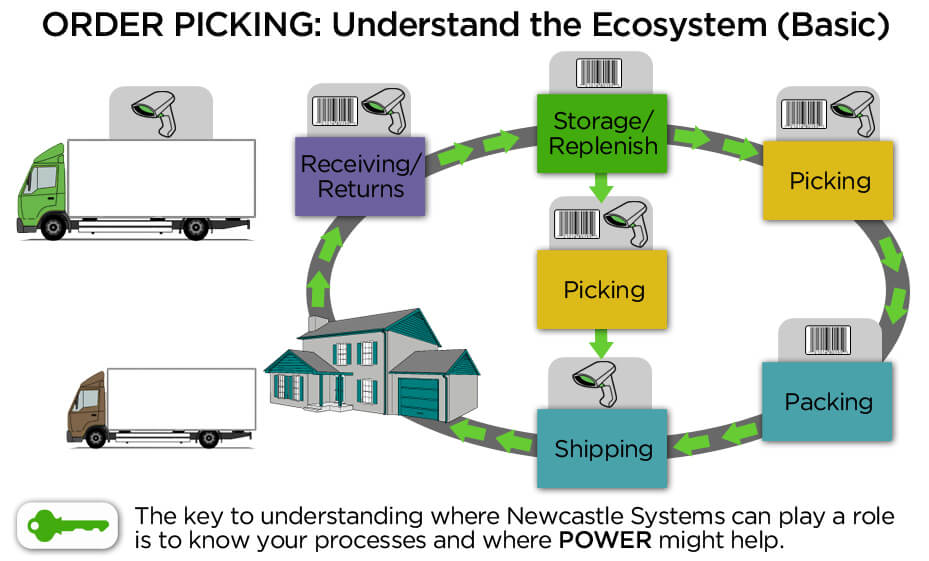
Order picking methods are defined in terms of: (a) pickers per order - the number of pickers that work on a single order at one time; (b) lines per pick - the number of orders a single item is picked for at one time; and (c) periods per shift - the frequency of order scheduling during one shift.
Order Picking Methods Include:
1. Discrete Order Picking
The most common type of order picking because it is basic and simple to understand.
When employing a discrete order picking methodology, one order-picker picks one order, one line at a time.
Additionally, there is only one order scheduling window during a shift. Therefore, orders are not scheduled and may be picked at any time on a particular day.
The advantages of using this method of order picking are: simplicity, ideal for paper based picking, provides fast response time for order fulfillment and can easily track order picker accuracy. However, this is the least efficient methodology as it requires a significant amount of travel time compared to other methods. (This is where a cart with built in power can help)
2. Zone Picking
Order pickers are assigned a specific and physically defined zone in the pick area. The picker assigned to each zone is responsible for picking all of the SKUs located in the zone for each order. In the event that an order requires SKUs that are located in multiple zones, the order is filled after it passes through each zone.
This is also referred to as the "pick and pass" methodology. In zone picking there is only one scheduling period per shift. This means there is a cutoff point for orders to be queued into the order picking process and any order received after that cutoff point will get fulfilled during the next shift.
3. Batch Picking
Batch picking is when one picker picks a group, or batch, of orders at the same time, one SKU at a time.
This is advantageous when there are multiple orders with the same SKU. When that occurs, the order picker only needs to travel to the pick location for that specific SKU once, in order to fill the multiple orders.
The main advantage for choosing this method is reduced travel time, which increases productivity. Batch picking is often used when the typical order profile has only a few SKUs (under four) and the SKUs physical dimensions are relatively small. Just as in zone picking, batch picking requires only one order scheduling window per picking shift.
4. Cluster Picking
Cluster picking is a methodology of picking into multiple order containers at one time. The containers could either be either totes containing order batches, discrete order shippers, or discrete order totes. There are two main piece picking systems that benefit from the use of cluster picking:
- Pick to cart operations, in which, a cart would be loaded with multiple totes or shippers and the picker will make one pass through the pick zone and sort to the pick containers, thereby avoiding unproductive travel.
- Vertical lift modules (VLM) or carousel operations utilizing the independent zone picking technique, the picker would setup the pick container batch, this would initiate the mechanized pick modules, and the items would be sorted to the proper pick container. This technique is used to optimize the VLM & carousel pods by limiting the number of machine cycles.
5. Wave Picking
Wave picking is very similar to discrete picking in that one picker picks one order, one SKU at a time. The main difference is the scheduling window. In discrete picking, there is not a scheduling window whereas in wave picking there is. Orders may be scheduled to be picked at specific times of the day, which is usually done to coordinate and maximize the picking and shipping operations.
6. Zone-Batch Picking
This is a combination of methods in that pickers are assigned a zone, just like traditional zone picking, however they are also directed to batch pick within their zone. Since both zone picking and batch picking have a scheduling window, then zone-batch picking does too.
7. Zone-Wave Picking
Zone-Wave Picking is a combination of methods in that pickers are assigned a zone and each picker within their zone picks all of the SKUs for all orders that are stocked in their zone, one order at a time with one scheduling window per shift.
8. Zone-Batch-Wave Picking
The most complex combination of all of the order picking methodologies. Each picker is assigned a zone and picks all SKUs for orders stocked in the assigned zone. Additionally, the picker picks more than one SKU at a time and there are multiple scheduling windows per shift.
Here is an overview of ordering picking methods and the number of picks per man hour:
Every operation manager has a high priority to minimize walking.
Minimize selector walking by:
1) Picking from both sides of the aisle, use small pick facings.
2) Placing slow-moving items on side aisles which are entered only when needed.
3) Picking many smaller orders in one trip (batch picking).
And the last method to minimize walking is by using a mobile pick cart with portable power built in. At Newcastle Systems, we provide the latest technology for productivity with mobile carts with built in power supplies which minimizes walking. Get immediate access to our new Picking Cart Guide here.
Comments
Post a Comment